Higher Efficiency with Reduced Cost
The GNSS and RTK-based grade control system features a 3D reference model, updates cut & fill workload, and displays excavator and bucket
position in real time, so operators of all skill levels can easily achieved accuracy of 3cm.
Application Scenarios
The 3D visual guidance enables operators of all levels to view the real-time working processes.
Entry-level operators will no longer have to check the depth and slope repetitively.
SPECs
Control Terminal
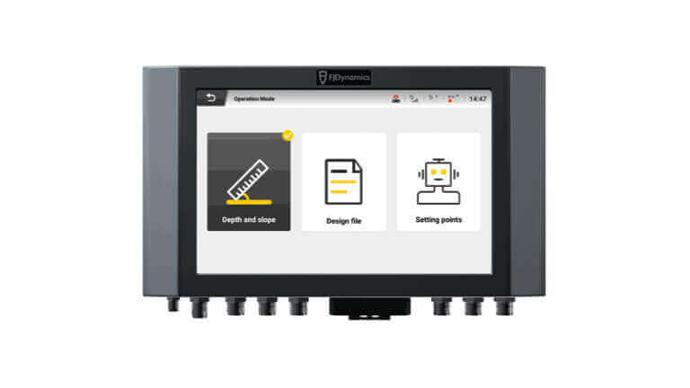
-
Human Machine Interface (HMI), control and display terminal of the excavator. The size is 10.1”. Users can view and control the status of the excavator and bucket.
-
Size
300 x 190 x 43 mm
-
Screen
10.1” LED Touchscreen
-
Signals
Radio, Positioning Satellite, 4G
-
Working Temperature
-30℃ – +70℃
-
Waterproof Rate
IP65
-
Power Supply
10-30 V
-
Accuracy
±3.0 cm
-
Power Supply
12-24V
Attitude Sensor Modules
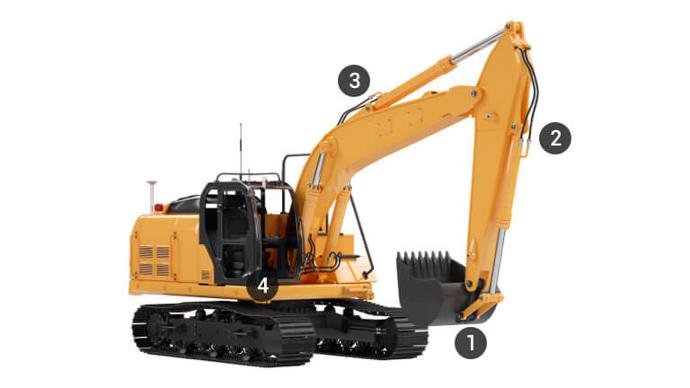
-
Obtain attitude information. The info will be transmitted to the control terminal, and the coordinates of the excavator bucket teeth are finally obtained through calculation. For general excavators, we have a total of four attitude sensors:
-
1. Excavator Platform Attitude Sensor
2. Boom Attitude Sensor
3. Stick Attitude Sensor
4. Bucket Attitude Sensor
-
Range
Pitch ±70°, Roll ±180°
-
Max Angular Velocity
≤ 400°/s
-
Working Temperature
-40℃ – +85℃
-
Waterproof Rate
IP67
-
Power Supply
4.9 – 32 V
Shqyrtime
Ende pa shqyrtime.